According to different grinding methods, we can divide the ball mills into dry ball mills and wet ball mills.
The field of application of wet ball mills is wider, but under certain conditions or for materials with special properties, dry ball mills are also indispensable grinding equipment.
So which materials are suitable for wet ball mills and which materials are suitable for dry ball mills?
Besides using different materials, what is the difference between dry ball mills and wet ball mills?
This article will give you the answer.
Applicable materials for dry ball mill
Under normal conditions, the ball mill is suitable for various metal ores, non-metal ores, etc.
Including materials that react with water, such as building stones such as concrete and marble, or products that require storage and sale in powder form.
Also, if the processing plant is in an arid area and water resources are limited, dry ball mills can be used for water saving reasons.
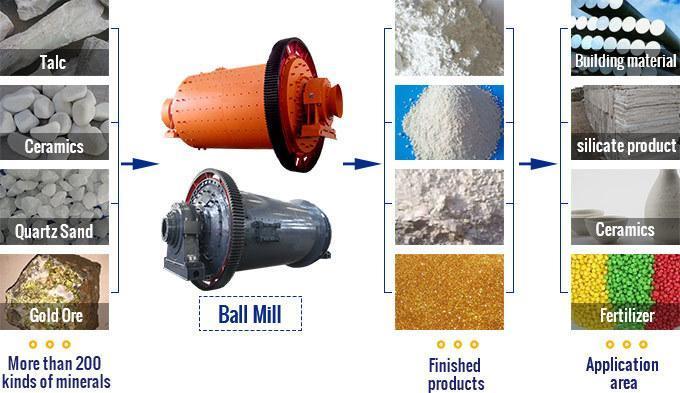
Applicable materials for wet ball mill
The wet ball mill has a wide range of applications and can process a variety of metallic and non-metallic minerals.
Common ones include gold ore, silver ore, copper ore, iron ore, molybdenum ore, phosphate ore, feldspar ore, fluorite ore and so on.
Wet ball mills can be used as long as the material meets water without compromising the quality of the product. Minerals that need to be sorted are usually processed using wet ball mills.
It should be noted that when using a wet ball mill, it is necessary to determine the ratio of steel balls, materials and water by enrichment tests to ensure the perfect grinding effect.
As for the choice of grinding equipment, it still depends on the subsequent operation of the ball mill, the nature of the product and the cost of production.
Dry grinding ball mill adopts lattice plate tail discharge, discharge is smooth, no lifting and grinding phenomenon, the cylinder does not need cooling, the service life is long, and the failure rate is small.
Wet ball mills offer superior performance, higher grinding efficiency and lower mineral moisture requirements. In addition, they have less auxiliary equipment and simple material handling devices, so the investment is about 5-10% less than dry ball mills. ...
In terms of the economic benefits of grinding operations, most concentrators will use wet ball mills as wet ball mills are easily adaptable to materials, can be produced continuously, and have a large grinding ratio. Wet ball mill has higher fineness and better enrichment effect.
In addition to the different materials used, dry ball mills and wet ball mills have some differences in the principle of operation and design:
Difference in the principle of operation:
In dry ball mill operation, the material is spiraled evenly into the first hopper of the mill through a hollow feed shaft from a feed device. The hopper has a stepped or corrugated coating and is equipped with steel balls of different specifications. The centrifugal force generated by the rotation of the ball mill drum lifts the steel ball to a certain height and then falls, crushing and crushing the material.
After the coarse grinding of the material in the first warehouse, the second warehouse is accessed through a single-layer partition. The warehouse is equipped with flat liners and steel balls of various characteristics for further grinding of the materials. Suitable materials are discharged through the discharge grate to complete the grinding operation.
The principle of operation of a wet ball mill is more or less the same as a dry ball mill, but there are some differences. Ball mill for wet grinding must add the appropriate amount of water or absolute ethanol during the grinding process, which means there are certain requirements for the grinding concentration. The amount of water is determined by the nature of the material. Suitable materials are discharged from the shaft through the discharge section and unskilled materials are returned to the ball mill for wet grinding.
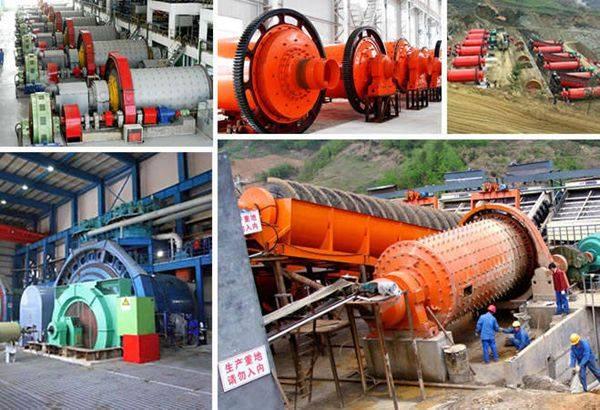
Structural difference
Both dry ball mill and wet ball mill include feed part one, exhaust part, rotating part, transmission part (gearbox, small transmission, motor, electric control) and other main parts.
The difference is that the dry ball mill is more complex than the wet one. Its outlet has a straight cylindrical shape and is equipped with an exhaust device, exhaust pipe and dust collector. is determined by its principle of operation. The liquid ball mill has a simple design and requires no additional accessories.The drain opening is tube-shaped and a screw device is integrated for easy draining.
I guess you have already figured out the difference between dry ball mill and wet ball mill from the detailed introduction above. Therefore, when choosing equipment, one should not only take into account the applicability of materials, but also fully take into account the principle of operation and design of the equipment. If you are still unable to make up your mind, you can also call our hotline for advice.
You can leave a message online or contact CLIRIK directly:
Email: sales@clirik.com
WhatsApp: +8613512155195/+8613917147829
FAQ
Who we are?
Shanghai CLIRIK Machinery Co.,Ltd. has been committed to the field of ultra-fine powder grinding machines for 20 years.
CLIRIK has a first-class manufacturing base with standardized and intelligent production lines.
CLIRIK's professional R&D, sales, installation and after-sales teams have provided door-to-door services to more than 100 countries and regions.
Which models can be selected for processing ultra-fine powder?